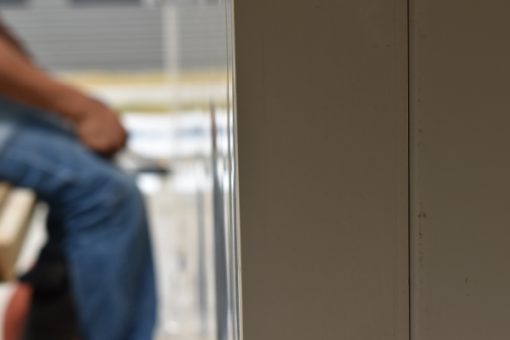
Modular Construction: Permanent and Relocatable
Modular (or prefabricated) construction is constantly seeking to meet the economic and functional demands of each sector. That is why it has managed to adapt to the temporary use of a building thanks to its structural versatility.
Permanent Modular Construction
Permanent Modular Construction (PMC) is an innovative and sustainable construction delivery method that uses off-site manufacturing techniques to prefabricate single or multi-story complete building solutions in deliverable module sections. PMC modules can be integrated into site-built projects or as a turnkey solution and can be delivered with installations, fixtures and interior finishes in less time, with less waste and greater quality control compared to projects using just the site built construction. Recent research has been done that supports the fact that modular construction is an efficient construction process and ready to help the growth of the construction industry.
“Off-site manufacturing of construction components provides more controlled conditions and allows for better quality and precision in component manufacturing.” – National Institute of Standards and Technology and the National Research Council
Relocatable buildings
A Relocatable Building (RB) is a partially or fully assembled building that meets applicable codes or state regulations and is constructed in a building manufacturing facility using a modular construction process. Relocatable buildings are designed to be removed or reused multiple times and transported to different construction sites. They are used for schools, construction site offices, clinics, commercial spaces, and anywhere a relocatable building can meet a temporary space need. These buildings offer fast turnarounds, ease of relocation, project reconfiguration, accelerated depreciation schedules, and tremendous flexibility. Relocatable buildings are not permanently affixed to real property, but are installed in accordance with the manufacturer’s installation guidelines and local code requirements. These buildings are essential in cases where speed, temporary space and relocation capacity are necessary.